Running for days straight makes even reliable industrial chillers fall inefficient in cooling.
After all, these chillers are machines that need proper maintenance for safety and optimum output.
This is why a chiller safety checklist is a must for the operators and maintenance team to follow.
Before learning more about the checklist, let us know the common chiller issues that lead to downtimes.
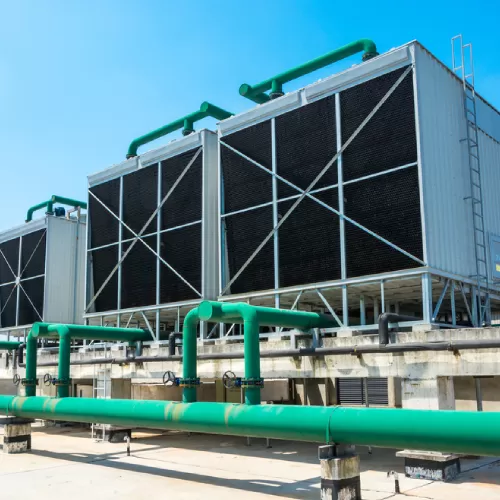
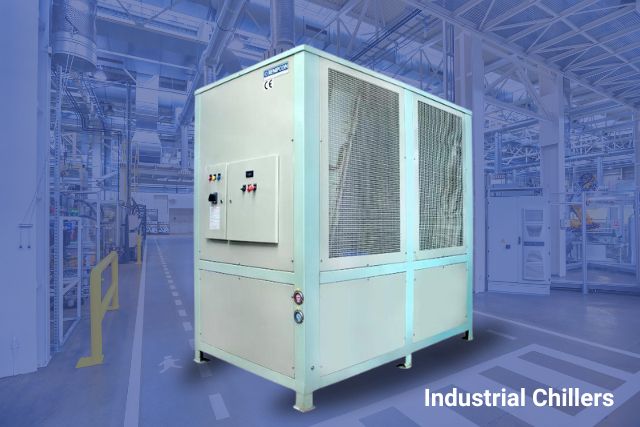
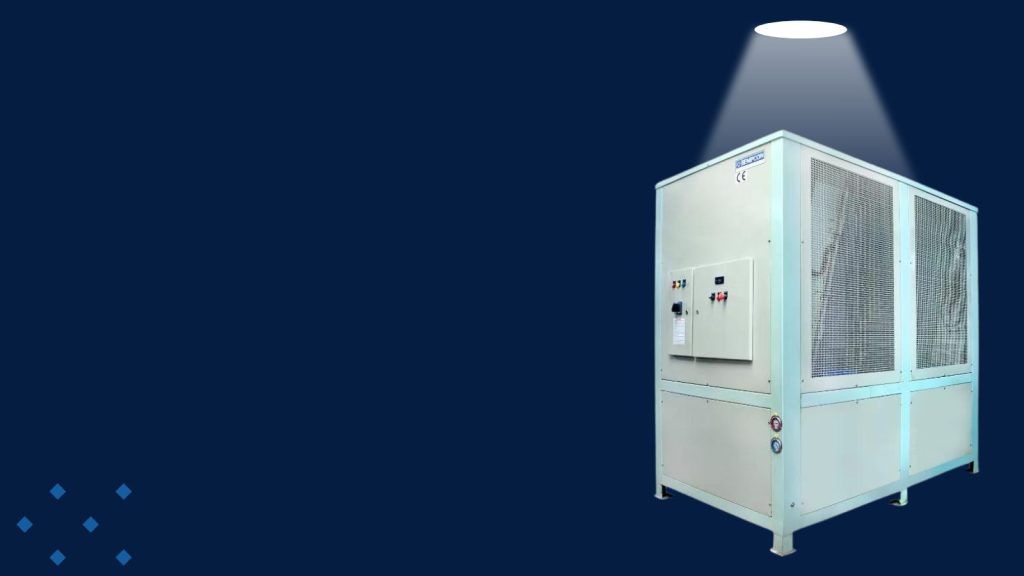
Common Chiller Signs You Must Know and Identify
Operational chillers often give tell-tale signs that operators neglect. These common signs are:
- Gradual Increase in Pressure
A steady rise in pressure in the condenser suggests issues related to improper water flow rates or trapped air and moisture.
- High Approach Temperature
When the temperature difference between the return and supply water, it indicates contaminants and unwanted depositions in the condenser and evaporator tubes.
- Refrigeration Load Limitation
The chiller fails to reach the cooling capacity it used to deliver. This sign may indicate improper flow, leakage, or migration of refrigerant.
There are other signs like sensor malfunctioning, improper outlet of hot air, etc that signify major issues in an industrial chiller system.
Chiller Safety Checklist: A Concise Table for Quick Follow-up
To avoid such issues, designing a chiller maintenance checklist is mandatory.
Task | Action |
Manufacturer guidelines | Review and follow specific maintenance needs. |
Clean Coils | Remove dirt, debris, and scale buildup. |
Lubricate Moving Parts | Apply lubricant to bearings, motors, and fans. |
Check Refrigerant Levels | Test and top-up refrigerant when necessary. |
Inspect Electrical Components | Ensure proper operation of controls and sensors. |
Test Water Quality | Monitor water chemical levels and quality. |
Calibrate Temperature/Pressure | Adjust based on seasonal needs. |
Inspect Seals and Insulation | Check for damage and heat loss prevention. |
Vibration Analysis | Detect and address excessive vibration. |
Test Safety Systems | Ensure alarms and shutdown systems work. |
Follow this chiller maintenance checklist for better results. Here is an elaborate version of this checklist for your convenience.
A Vivid Chiller Maintenance Checklist for Safety
CA chiller safety checklist is a prime factor that enhances its longevity and efficiency when followed. A well-structured checklist, irrespective of the chiller type, can help you keep the components functioning properly.
Here is a general list you can follow and customise.
Gather and Follow the Manufacturer’s Guidelines
Always keep the manufacturer’s guidelines handy when you are about to check a chiller’s components for maintenance. Follow the guidelines to know how to keep your chillers safe and functioning properly.
Condenser and Evaporator Coil Cleaning
Clean the evaporator coils and condensers regularly to remove debris, dirt, and scale deposition. Clean coils are efficient in carrying heat and prevent early breakdowns.
Moving Parts Lubrication
A modern chiller design comprises moving parts like bearings, motors, and fans. These moving parts need proper lubrication from time to time to avoid the risk of malfunctioning and overheating.
Refrigerant Level Check
Refrigerant levels determine the efficiency of an industrial chiller. Checking a refrigerant’s level periodically will help determine leakage and other relevant issues.
Electrical Component Inspection
Examine the electrical connections, controls and sensors for an optimum operational output. These components must function properly and must be free from issues to enhance safety.
Water Quality Test
Chemicals tend to corrode the components whereas suspended particles deposit on conducting surfaces. These hindrances contribute to inefficient cooling of the industrial chillers. Regular water quality testing can stop corrosion, scale, and even microbial growth.
Pressure and Temperature Calibration
Pressure and temperature controls should be checked and calibrated regularly. These adjustments based on seasonal changes lead to efficient usage of industrial chillers and reduce energy bills.
Insulation and Seal Inspection
Check the seals and insulations throughout the chiller system. Replace damaged seals and insulations to avoid energy loss.
Vibration Analysis
Analyse the vibration of a chiller to detect internal mechanical problems early. Excessive vibration indicates compressor alignment and rotating component issues.
Safety System Test
Check all the safety systems like alarms, emergency shutdown procedures, and interlocks. Regular testing of these fixtures will keep the chiller system and operators safe from malfunctioning.
Leak Check
Check for refrigerant, water, and oil leaks to increase efficiency and avoid safety hazards.
Condenser and Evaporator Pressure Check
Measure and verify the condenser and evaporator pressure frequently to maintain a recommended range.
Following this list for regular maintenance will increase your industrial chiller’s lifespan. Fewer instances of repairing and downtime will automatically save your resources.
Further Reading: Chiller Maintenance Checklist
Tempcon: Your Ultimate Chiller Maintenance Partner
Chiller troubleshooting is a job for expert technicians. Don’t have a maintenance team? Don’t worry as Tempcon has got you covered. We provide after-sales maintenance services for industrial chillers. Let us handle your chiller maintenance and give you the best support.
Contact us today for further assistance!