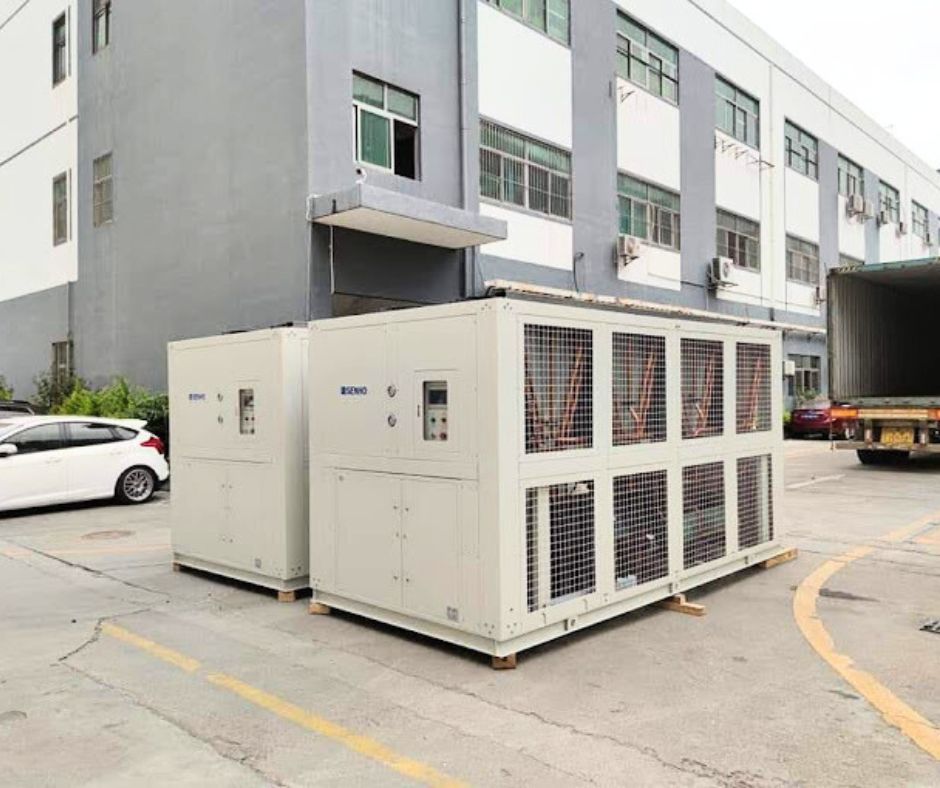
Infrastructure
As a leading industrial chiller manufacturer in India, we have established state-of-the-art facilities. Our robust organization ensures efficient and high-quality production. Our current manufacturing facility spans over 12,600 square feet in the prominent Kasba Industrial Estate in West Bengal, Kolkata. Being well-known for its industrial prowess, this estate makes it an ideal location for our operations.
We are also establishing an additional manufacturing facility in 24 Pgs (S) in the coming year. This new facility will cover an expansive area of 30,000 square feet. Our production capacity will now increase, and this new estate will allow us to meet our customers’ growing demands.
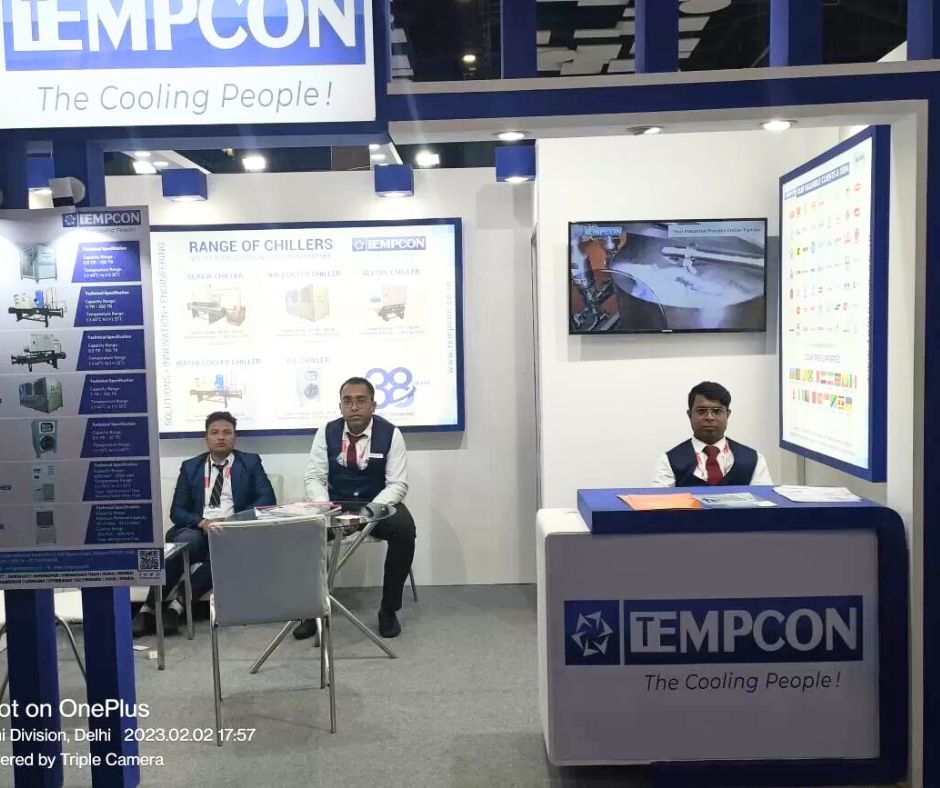
Team
Tempcon takes pride in having a highly skilled and dedicated team. Our workforce of 40 professionals comes from diverse backgrounds. We are highly inclusive of members from different communities.
We have IITans, Btech Engineers, Diploma Engineers, MBA Graduates, and Chartered Accountants (CA) on our team. With their expertise and knowledge, we strive for excellence in every aspect of our chiller manufacturing process.
We are committed to delivering top-notch products and services. With our well-equipped facilities, skilled team, and advanced technology, we aim to exceed our customers’ expectations and contribute to the growth of various industries.
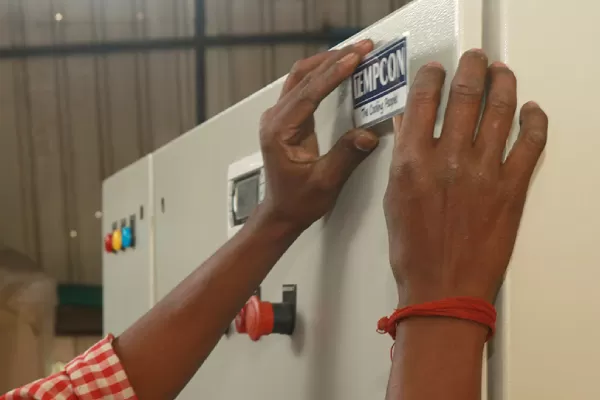
Quality Assurance
We at Tempcon give utmost importance to the quality and performance of our products. To ensure that our products are up for the most challenging tasks, we maintain in-house testing benches for all our industrial chillers. Each of the process chillers that goes out into the market undergoes rigorous testing on these benches.
Some of our common testing benches are:
Air-Cooled Chiller Testing Bench: It is designed to test air-cooled scroll chillers and air-cooled screw chillers. It is capable of testing chiller units ranging from 1 TR to 100 TR capacity.
Water-Cooled Chiller Testing Bench: It is designed to test water-cooled scroll chillers and water-cooled screw chiller units. It can handle cooling systems of up to 350 TR capacity.
Low-Temperature Brine Chiller Testing Bench: Brine chillers operate at very low temperatures, so they require special testing. This bench is equipped to test chiller units that reach extremely low temperatures. It is capable of testing cooling systems that reach temperatures as low as (-)40°C.
Nitrogen Pressure Testing Bench: We maintain two nitrogen pressure testing benches to ensure the integrity of our products.
Tools
Automatic Tube Bender: It is used to bend tubes and pipes to achieve the desired chiller design. This bender can bend tubes ranging from 1/4″ to 2 5/8″ in diameter.
Two-Stage Vacuum Pump: Creating a vacuum environment for effective leak testing is vital in chiller manufacturing. To ensure effective vacuuming during production, we have 15 two-stage vacuum pumps. Our two-stage pumps are superior to the one-stage pumps that our competitors use.
Digital Vacuum Gauge: To measure the vacuum in the above-mentioned vacuum pumps, we have 15 digital vacuum gauges. They give accurate pressure measurements so we can monitor the safety of the production process.
Electronic Digital Manifold: Manifolds are used to combine or split fluid streams, control flow direction, and regulate pressure. That’s why we have five units of electronic digital manifolds. Through these, we can monitor and control chiller refrigerant flow during production.
Leak Detection Tanks: We have three dedicated tanks for detecting and addressing any leaks in our equipment. All our products undergo leak detection before being set out on the market.
Electric Welding Machines: Welding is of utmost importance to keep the parts of a chiller connected. To ensure a strong connection, we use electric welding machines. We possess 2 of these for efficient and reliable welding processes.
Argon Welding: For precision welding, we have one Argon welding machine. It is used for complex and high-quality welding requirements in our cooling systems.
Brazing Systems (Oxygen and LPG): To connect different types of metals together, we have four sets of brazing systems. These utilize both oxygen and LPG for strong and durable joints.
Fabrication Infrastructure
CNC (Sheet Cutting and Punching):
CNC (Sheet Cutting and Punching): We design custom chillers to fit the size requirements of our clients. And for that, we use our CNC machine. It does accurate sheet cutting and punching so that we can design chillers of all shapes and sizes.
Automatic Bending Machine:
Bending sheets and pipes are essential for a chiller design. And they have to be accurate, too. That’s why we use two automatic bending machines. They are capable of achieving consistent and precise bends.
Powder Coating Paint:
We offer powder-coated tank options in our chillers. To achieve this epoxy powder coating, we have a 7-tank process and a heat chamber. They enable us to apply durable powder coating finishes to the mild steel tanks.
Software
25 years experience
For resource planning and management, we utilize Microsoft 360 and Analysts software. They allow us to keep track of all our chillers, from order placement to their delivery and maintenance. We believe in tracking the complete lifecycle of our products.
Drawing Design:
When it comes to drawing and design, we trust no one better than the AutoCAD 2020 tool. It is versatile and allows us to create detailed and precise equipment designs.
Strong service network
Tempcon is the best chiller manufacturer in India for a reason. We don’t just deliver industrial chillers; we also cater to our customer’s needs post-delivery. We have established a strong service network of over 20 service engineers so our customers can get the help they need.
These engineers are located in strategic locations such as Noida, Indore, Patna, Mumbai, Bangalore, Jamshedpur, Bhubaneswar, Guwahati, Doha, Dhaka, and Kathmandu. This ensures that we can provide prompt and reliable support to our customers when and where they require it.
To facilitate our service operations, we have the following facilities in place:
A dedicated service van equipped with the necessary tools and equipment.
Specialized equipment for specific service tasks: Water-Cooled Condenser Descaling Machine, Air-Cooled Condenser Cleaning Machine
A service kit containing essential items for on-site breakdown attendance. We have ten such sets readily available for deployment.
FAQ
Tempcon specializes in creating custom industrial chillers by leveraging its advanced infrastructure and skilled team. Key features include:
- A 12,600 sq. ft. manufacturing facility in Kolkata, West Bengal.
- Upcoming 30,000 sq. ft. unit to meet growing demands.
- CNC machines for precise sheet cutting and punching.
- Automatic tube benders for accurate designs.
- Advanced tools for leak detection and vacuum testing.
Tempcon ensures top-quality products through rigorous in-house testing. Key quality assurance tests include:
- Air-cooled chiller testing for 1–100 TR units.
- Water-cooled chiller testing for up to 350 TR systems.
- Low-temperature brine testing for (-)40°C systems.
- Nitrogen pressure tests with dedicated benches.
- Comprehensive leak detection before market release.
Tempcon’s service team includes over 20 engineers strategically located across cities like Noida, Mumbai, and Bangalore. Equipped with specialized tools and service kits, they ensure prompt support for customers.
Tempcon’s team offers comprehensive post-delivery services across the Indian states. Our services include:
- Quick on-site repairs with fully equipped service kits.
- Cleaning and descaling for air-cooled and water-cooled condensers.
- Routine maintenance using specialized tools and dedicated service vans.