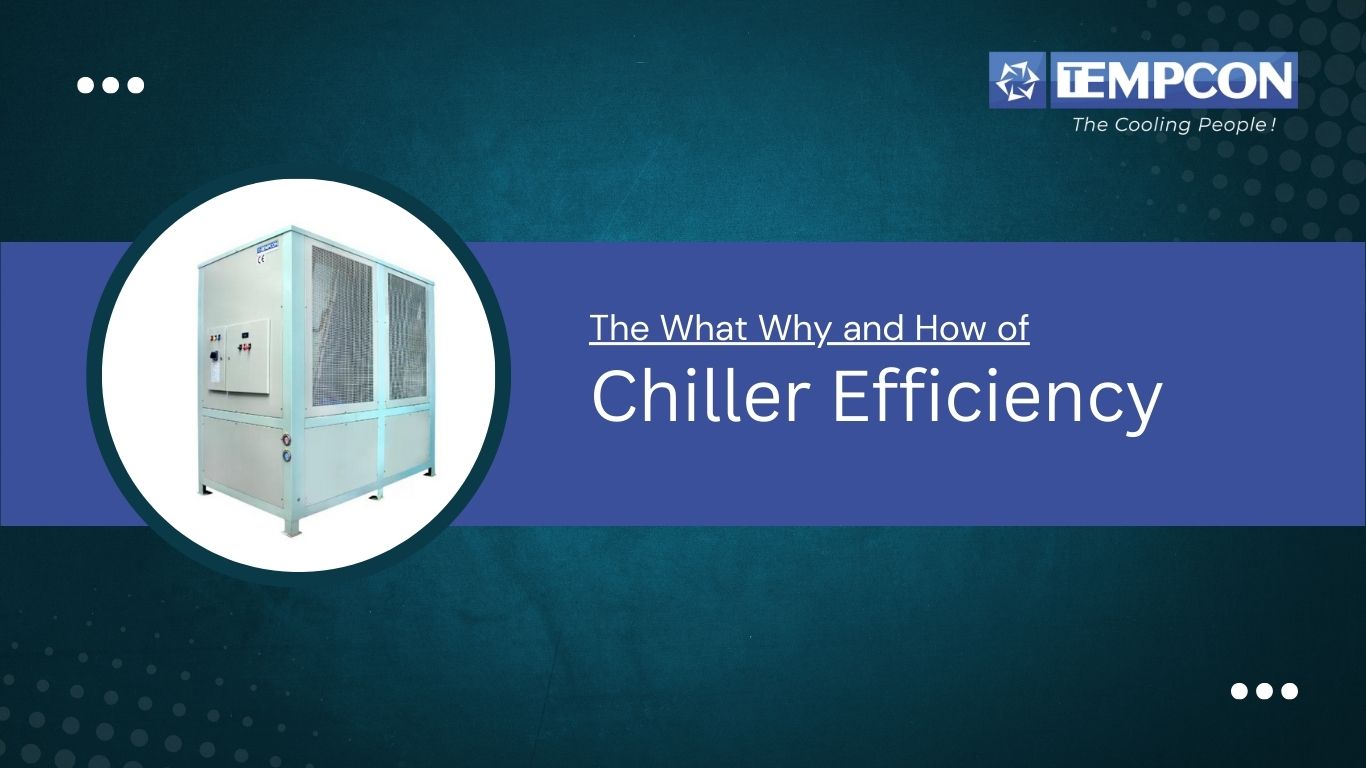
Industrial chillers maintain an ambient temperature required to keep equipment, industrial processes, and products safe. Calculating the efficiency of chiller before installation can prevent overheating, promote smooth operations, and improve energy efficiency.
Here is a concise explanation of the terms associated with chiller efficiency calculation.
Calculating Chiller Efficiency: Industrial Terms Explained
These terms help measure performance, energy use, and overall effectiveness.
Chiller Efficiency Calculator
Calculate key performance metrics for industrial chillers to optimize energy usage and cooling performance.
Cooling Load (kW/ton)
Measure heat removal capacity
The cooling load measures the amount of heat a chiller removes per unit of refrigeration capacity. Calculating chiller efficiency kW ton helps industries size their chillers correctly to match cooling demands.
100 × 3.517 = 351.7 kW
This formula for chiller efficiency kW ton calculation will help you identify the right chiller design for your industrial setup.
Coefficient of Performance (COP)
Measure energy efficiency ratio
COP explains how efficiently a chiller uses electrical energy to cool. A higher COP means better efficiency and lower electricity use.
200/50 = 4
Energy Efficiency Ratio (EER)
BTU/W ratio measurement
EER is a ratio that measures cooling efficiency but uses BTU and watts in place of kilowatts. It is commonly used in HVAC systems to compare energy consumption.
120,000 / 3,000 = 40
IPLV & NPLV
Part-load value measurements
IPLV (Integrated Part Load Value) and NPLV (Non-Standard Part Load Value) measure chiller efficiency at varying loads instead of full capacity. These ratings help predict real-world performance since chillers rarely run at 100% load all the time.
If actual operating conditions differ from standard test conditions, the chiller may have an NPLV of 5.5 instead.
These values help industries choose the most efficient chiller for real-world conditions.
Interactive Calculator
Calculate efficiency metrics for your chiller
Chiller Efficiency Results
Efficiency Rating
Why is Calculating Chiller Efficiency Mandatory?
Measuring chiller efficiency is important for industries. Here’s why:
- Energy Savings – Efficient chillers use less electricity and lower operational costs.
- Lower Carbon Footprint – Less energy consumption reduces greenhouse gas emissions.
- Equipment Longevity – Tracking efficiency helps with timely maintenance and reduces downtime.
- Regulatory Compliance – Calculating chiller efficiency helps meet regulatory standards.
- Optimized Performance – Knowing efficiency helps in adjusting settings for better output.
- Cost Control – Unchecked inefficiency leads to higher electricity bills and unexpected repair costs.
Thus, industries can reduce expenses, meet regulations, and extend equipment life by tracking chiller efficiency.
Factors to Consider When Calculating Chiller Efficiency
Understanding these factors will help industries reduce energy costs and improve performance.
Cooling Load
The amount of heat a chiller removes is governed by its efficiency. If a chiller is too large for the job, it will cycle on and off and waste energy. If it’s too small, it will run constantly and lead to wear and higher costs.
Power Consumption
The electricity a chiller uses impacts efficiency. A more efficient chiller provides the same cooling while using less power. Measuring power input helps track performance.
Operating Conditions
Temperature and humidity affect efficiency. Chillers work best in stable conditions. Extreme heat, cold, or moisture can lower performance.
Part-Load Efficiency
Chillers don’t always run at full capacity. Efficiency ratings like IPLV and NPLV measure how well they perform at lower loads. A chiller that adjusts its cooling based on demand saves more energy.
Maintenance and Cleaning
Dirty coils, clogged filters, and poor refrigerant levels decrease efficiency. Regular servicing keeps the chilling operation smooth.
The best practice is to hire a reputed Industrial Chiller Manufacturer to calculate the cooling capacity for an industrial unit, installation, and periodic maintenance.